The housing industry is witnessing an unprecedented demand for innovation and financial efficiency as the need for affordable housing continues to surge. Labor shortages and escalating construction costs pose significant challenges. However, within this demanding landscape, Structural Insulated Panels (SIPs) have been a proven solution, revolutionizing the way high-performance homes are constructed.
Despite their proven technology, SIPs have faced challenges in capturing the attention of mainstream builders and architects. SIPs offer a 21st-century approach to building, one that not only achieves cost neutrality but often proves more economical than conventional construction techniques. This is the first of a 3-part series exploring the undeniable advantages of SIPs through real-world case studies.
SIPA True Cost Bidding Tool (STCBT)
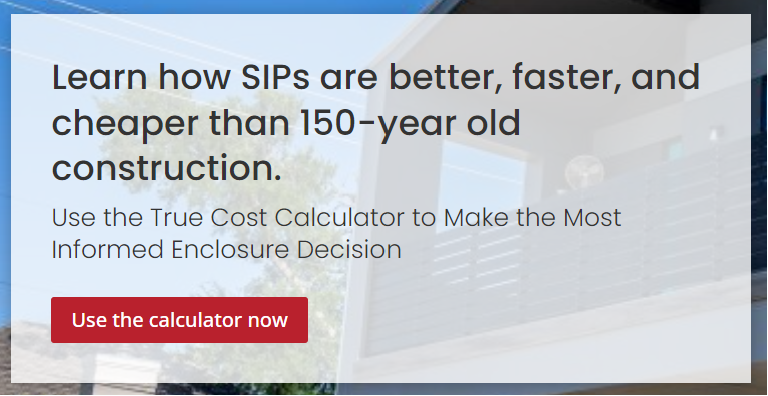
To overcome the challenges of introducing SIPs to builders and architects, the Structural Insulated Panel Association (SIPA) developed a bidding tool aimed at effectively conveying the value of SIPs’ advanced enclosure technology. The problem lies in the traditional bidding process, where SIPs were often reduced to a mere comparison of framing packages. To drive wider adoption of SIPs, it is essential to clearly illustrate the true cost benefits of these innovative panels, contrasting them with the age-old framing technology that has been in use for over a century.
And so, the SIPA True Cost Bidding Tool (STCBT) was created. This tool serves as a bridge between conventional framing and advanced SIPs, simplifying the process and providing clarity on the cost differential. In this 3-part series, we will discuss the real value creation that SIPs bring to the housing industry, highlighting case studies that showcase their distinct advantages over traditional construction methods.
Case Study: SIPs-Optimized Single-Family Production Home
Rob Howard, a seasoned expert in building science, embarked on a unique project to address workforce housing needs in Granite Falls, North Carolina, all while teaching building science at Appalachian State University. His residential development, known as Duke St. Cottages, stands out for its U.S. DOE Zero Energy Ready Home certification, making it a prime candidate for this case study.
The home is a two-bedroom, two-bath dwelling with 1,600 square feet of conditioned living space. What’s truly remarkable is its price tag - a mere $199,900. To put this into perspective, the current median home price in North Carolina stands at a significantly higher $363,000. This project was designed from the ground up with SIPs wall and roof construction in mind. The utilization of SIPs in the roof design not only created a conditioned space but also offered additional loft storage for half the home and a sloped ceiling for the other half. The design meticulously adheres to two-foot dimensions to minimize waste.
As this project was constructed using SIPs, the actual costs for SIPs were compared to estimates for conventional framing, based on industry cost data. The initial baseline comparison focused on comparing SIPs and framing bid packages. Subsequently, a true cost analysis was conducted, factoring in cost savings related to insulation, air sealing, finishes, quality and cycle time. Added value assumptions were made concerning enhanced strength, resilience, storage and high ceilings. These cost and value assumptions were rigorously reviewed with Rob Howard, the project’s creator.
The results of the Howard Building Science case study reveal the following:
Baseline Comparison: SIPs incurred a significant $14,000 cost premium, which was 56% higher than conventional framing.
True Cost Analysis: The SIPs-optimized project showcased a new cost and added value advantage of $35,291, a staggering 65% lower cost than conventional framing. This highlights the immense significance of integrating SIPs into the project design.
The Howard Building Science case study demonstrates the considerable benefits of incorporating SIPs into the construction process, not only in terms of cost savings but also in added value, making it a compelling choice for builders and homeowners.
The Solution: SIPs for High-Performance Enclosures
SIP construction offers a revolutionary approach to creating high-performance enclosures, providing several key benefits. This video by Sam Rashkin, Chief Architect from the U.S. Department of Energy and creator of the ENERGY STAR for Home Program and the Zero Energy Ready Home Program, outlines the advantages to using SIPs.
The Added Value and the Cost Savings of Using SIPs
Beyond cost-effectiveness, SIPs provide value that significantly enhances the overall quality and functionality of homes. Let's not forget the tax credits and incentives available for high-performance enclosures. Eligibility for a 45L tax credit
Unlock the Power of SIPs in Your Project
SIPs are undeniably transforming the way we build, offering unmatched cost savings, energy efficiency, and resilience for high-performance homes. Whether you’re a builder, architect, or homeowner seeking innovation and value, SIPs represent a revolutionary leap forward in construction technology. To explore further how SIPs can elevate your construction project, we encourage you to dive deeper into SIPA’s resources:
SIP Project Library: Discover a wealth of SIP residential projects showcasing high-performance and energy metrics in SIPA’s Residential SIP Project Library.
SIPA True Cost Bidding Tool (STCBT): Gain insights into the real cost benefits of SIPs compared to conventional framing with the SIPA True Cost Bidding Tool.
Tell Us About Your Project: Share details of your project with us and learn how SIPs can be tailored to meet your specific construction needs.
By harnessing the advantages of SIPs, you can not only achieve cost-efficiency but also create resilient, energy-efficient homes that stand the test of time. Embrace the future of construction with SIPs!