Adaptive and Practical Building Technologies to Meet Modern Homeowner/Builder Needs
It’s 2022 and wildfires are a regular occurrence in the western United States. Every year, thousands of people are displaced by the looming threat of these fires and months of poor air quality disrupting their pristine – oftentimes remote – residential areas. Governments and communities have acted by strengthening building codes in these locations to ensure contemporary buildings are fire-resistant and won’t act as kindling. The International Code Committee’s International Wildland-Urban Interface Code establishes a set minimum standard to reduce the loss of property from wildfires with ignition-resistant construction requirements. Much of California and Central Oregon falls into this ‘wildlands’ category, meaning design professionals and builders require materials outside the tinder box.
Structural insulated panels (SIPs) are a building envelope technology offering the most comprehensive array of safety and energy benefits to builders, designers and future occupants. Since the framing factor of SIPs is a fifth of a typical stick-frame home (with studs every 16 inches), SIPs require significantly less lumber from the project’s inception and they reduce thermal bridging (insulation gaps or air leakage points) by 60%. This results in increased comfort and better control over the indoor temperature as well as less wood, an expensive material with very low fire tolerance. SIPs are an exceptional building choice in wildfire-prone regions as they are self-extinguishing and fire-resistant. All EPS foam is treated with flame retardants along with some of the OSB; however, the flame barrier most depended on is the gypsum board layer. All together as an assembly, the material is tested for 1-hour fire rating.
Meet me on the roof
A SIP structure can achieve astonishing energy performance ratings because of the nearly airtight engineering of interlocking panels. This technology expands beyond the wall system and into the roof construction. Since SIP roofs do not require venting, this conditioned space can be used as attic storage without posing the fire risk of traditional attic spaces. Oftentimes, attic venting is the culprit for a house igniting in flames. That roofline venting provides an entrance for floating hot embers and the oxygen needed to fuel a fire. A SIP attic, however, is fully enclosed without entry points for wildfire debris or harmful smoke, not to mention insects and other pests.
SIP wall and roof/ceiling assemblies have been tested and passed the 1-hour fire rating (ASTM E119) demonstrating that occupants are safe up to one hour after the structure is exposed to fire. This fire-resistance rating is designed for building products and found that SIPs are flame retardant and self-extinguishing. The gypsum board exposed to the fire would not readily ignite and after it had caught fire, it extinguished when the flame was removed.
Later this summer, ICC NTA is conducting a 2-hour fire rating test on SIPs. Keep a pulse on SIPA’s Fire Performance content for updates.
Flame retardants and additional products
There are several different approaches to making SIPs more resistant to fire. Including an extra layer of gypsum board or sheet rock over the panel that’s been treated with flame retardants is a common fire precaution for SIP structures. The board acts as a 15-minute internal thermal protective layer. SIPA Technical Bulletin No. 2 offers a summary of fire precautions aligned with building code compliance.
To exceed building codes and ease homeowner concerns, each SIP manufacturer offers unique fire-resistant products specifically suited for their panels; however, EPS panels are always treated with flame retardants. For more information on these technologies and materials, contact a SIPA manufacturing member.
An award-winning, fire-resistant SIP example!
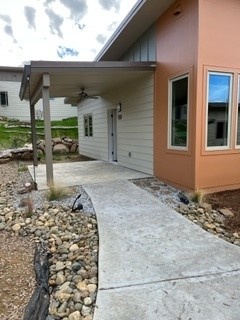
This 18-unit duplex community in Sonora, California incorporated SIPs and other measures to meet the realistic needs of occupants on this beautiful hillside. With annual threats of wildfires, these earth-toned SIP duplexes meet and exceed building codes, incorporating fire suppression design features throughout the structure. These features include:
- Excess thermal bridging was eliminated with the use of R-15 batt in the top chord of the truss beneath the R-28 SIPs providing a better-sealed R-43 assembly.
- Gable end walls go all the way to the bottom of the SIP panel, which provides all the overhangs without requiring additional framing.
- Exteriors are all HardiePlank, HardiePanel and HardieTrim for fire-proof exteriors while the roofs are all steel standing-seam roofing.
- The combination of HardieSiding and HardieSoffit along with all the tempered glass in the windows and the steel roof provide a fireproof exterior shell.
With solar panels on the garages only, these units will completely power themselves and their owners’ cars (two cars per unit at 10,000 miles per car per year). Once the entire south-facing roofs are fitted with solar panels, these 18 residential units will power themselves and an addition 54 average existing homes in the neighborhood.
This project is the well-deserved winner of SIPA’s 2022 Building Excellence Award in both the multifamily category as well as the overall high-performance residential winner. The panels for this project were manufactured by PremierSIPs and the project was designed by Zero Energy Plans, LLC.
Additional Resources:
SIPA Technical Bulletins
How SIPs Meet Building Codes and Standards
Healthy Indoor Air Quality (IAQ) Starts with SIPs